Avoiding Marring On Steel Pipe When Threading
-
- Posts: 302
- Joined: Mon Jun 25, 2012 12:13 pm
- Location: Wiltshire United Kingdom
Avoiding Marring On Steel Pipe When Threading
I'm using a vice same as the one in the attached pictures the vice jars bite into and marrs the pipe. Someone on the forum suggested using an old leather belt. I tried 3 turns around the pipe, gripped quite well but pipe still turned. I tightened up the vice as much as I could by hand. I'm reluctant to use a tommy bar to apply more pressure as might mess up the vice or crush the pipe. Is there any other method I could try to avoid marring the pipe?
Thanks.
Thanks.
Re: Avoiding Marring On Steel Pipe When Threading
My opinion only.
There is no way you can restrain the pipe without damage of some sort when using such a small area of contact. By design, that method of holding is intended to damage the pipe, and would be considered acceptable.
You can restrain pipe without marring by using a large area of contact. It can even be smooth, assuming you can apply enough pressure without damaging the holding device. Using padding with the device shown isn't likely to work.
Harold
There is no way you can restrain the pipe without damage of some sort when using such a small area of contact. By design, that method of holding is intended to damage the pipe, and would be considered acceptable.
You can restrain pipe without marring by using a large area of contact. It can even be smooth, assuming you can apply enough pressure without damaging the holding device. Using padding with the device shown isn't likely to work.
Harold
Wise people talk because they have something to say. Fools talk because they have to say something.
-
- Posts: 326
- Joined: Fri May 28, 2010 3:40 pm
- Location: Winchendon Mass. USA
Re: Avoiding Marring On Steel Pipe When Threading
If your pipe is reasonably round make a split clamp, 2 pieces of square stock bolted together with a spacer in between them bore a hole the size of your pipe remove spacer then clamp on your pipe it won't turn . I had to make a clamp like this when I had to replace the tie rod ends on my tractor, tie rods screwed into the steering cylinder so marks were not allowed.
Re: Avoiding Marring On Steel Pipe When Threading
You really need to get that split sleeve made, but lacking a lathe, try another approach.
Take a coupling that pipe size, split in half and file/grind out most of the threads.
If you have a press or stout bench vise (not a woodworker's vise!) force one half at a time onto the pipe.
A torch will assist, dull red heat at most. Too hot and you'll go past yield and there'll be no spring left.
Once you get the halves off the pipe, add some clearance to ease your work.
The best grip is when you first form, so maybe pry the half coupling off after you thread.
A couple notes.
Those pipe jaws are supposed to bite the pipe, just like pipe wrenches. A file removes the ridges, but not the pits.
If the pipe is equivalent to U.S. Sch.40, standard wall steel pipe, black, there is no way you are going to crush it with arm powered screw threads.
You could bend the drive bar on the screw of that unit using a cheater, once you put a few sandbags on the shelf to stop it chasing you around.
You have added a small chamfer/bevel to your pipe before threading, and applied regular liberal doses of cutting oil, yes?
Take a coupling that pipe size, split in half and file/grind out most of the threads.
If you have a press or stout bench vise (not a woodworker's vise!) force one half at a time onto the pipe.
A torch will assist, dull red heat at most. Too hot and you'll go past yield and there'll be no spring left.
Once you get the halves off the pipe, add some clearance to ease your work.
The best grip is when you first form, so maybe pry the half coupling off after you thread.
A couple notes.
Those pipe jaws are supposed to bite the pipe, just like pipe wrenches. A file removes the ridges, but not the pits.
If the pipe is equivalent to U.S. Sch.40, standard wall steel pipe, black, there is no way you are going to crush it with arm powered screw threads.
You could bend the drive bar on the screw of that unit using a cheater, once you put a few sandbags on the shelf to stop it chasing you around.
You have added a small chamfer/bevel to your pipe before threading, and applied regular liberal doses of cutting oil, yes?
-
- Posts: 302
- Joined: Mon Jun 25, 2012 12:13 pm
- Location: Wiltshire United Kingdom
Re: Avoiding Marring On Steel Pipe When Threading
How thick should the spacer be, how do I mount this clamp, please explain in more detail?duckman903 wrote:If your pipe is reasonably round make a split clamp, 2 pieces of square stock bolted together with a spacer in between them bore a hole the size of your pipe remove spacer then clamp on your pipe it won't turn . I had to make a clamp like this when I had to replace the tie rod ends on my tractor, tie rods screwed into the steering cylinder so marks were not allowed.
Thanks.
-
- Posts: 302
- Joined: Mon Jun 25, 2012 12:13 pm
- Location: Wiltshire United Kingdom
Re: Avoiding Marring On Steel Pipe When Threading
I'm quite friendly with a machinist does scale steam trains and stuff, has a quite big industrial lathe and a mill. Tell me more about this split sleeve so I can ask him to make one up for me? I'm threading the pipe fine now no problems, I'm adding quite a lot of cutting oil and breaking the chips. I didn't add a chamfer/bevel to the pipe.Carm wrote:You really need to get that split sleeve made, but lacking a lathe, try another approach.
Take a coupling that pipe size, split in half and file/grind out most of the threads.
If you have a press or stout bench vise (not a woodworker's vise!) force one half at a time onto the pipe.
A torch will assist, dull red heat at most. Too hot and you'll go past yield and there'll be no spring left.
Once you get the halves off the pipe, add some clearance to ease your work.
The best grip is when you first form, so maybe pry the half coupling off after you thread.
A couple notes.
Those pipe jaws are supposed to bite the pipe, just like pipe wrenches. A file removes the ridges, but not the pits.
If the pipe is equivalent to U.S. Sch.40, standard wall steel pipe, black, there is no way you are going to crush it with arm powered screw threads.
You could bend the drive bar on the screw of that unit using a cheater, once you put a few sandbags on the shelf to stop it chasing you around.
You have added a small chamfer/bevel to your pipe before threading, and applied regular liberal doses of cutting oil, yes?
Thanks.
Re: Avoiding Marring On Steel Pipe When Threading
"Tell me more about this split sleeve so I can ask him to make one up for me?"
It was described in the other thread you had asking about this, and similar to what Duckman describes in this thread, though his is a bit more work.
You make a close fitting hole in a piece of tube. The hole needs be at the largest tolerance of the pipe diameter....
Pipe is far from a precision material, it is not round, and the OD will vary. The best grip is the closest to pipe diameter.
If your sleeve is steel, then it need not be very thick wall, say around 4mm.
Brass, copper or looneyum need to be thicker.
One slit, lengthwise. The crush distance should not be greater than the kerf.
I mentioned a chamfer on the pipe end as some lots have hot saw ends, quite a burr that makes it hard to start the die.
If you buy pipe by the ton, best way to get it, unless you know and specify the connections beforehand.
It was described in the other thread you had asking about this, and similar to what Duckman describes in this thread, though his is a bit more work.
You make a close fitting hole in a piece of tube. The hole needs be at the largest tolerance of the pipe diameter....
Pipe is far from a precision material, it is not round, and the OD will vary. The best grip is the closest to pipe diameter.
If your sleeve is steel, then it need not be very thick wall, say around 4mm.
Brass, copper or looneyum need to be thicker.
One slit, lengthwise. The crush distance should not be greater than the kerf.
I mentioned a chamfer on the pipe end as some lots have hot saw ends, quite a burr that makes it hard to start the die.
If you buy pipe by the ton, best way to get it, unless you know and specify the connections beforehand.
Re: Avoiding Marring On Steel Pipe When Threading
I just recently posted in another VERY similar thread regarding what I have been told is called a "barrel vise", presumably in reference to removing rifle barrels without damage, and I'm told some of those verge on the impossible due to "clocking" and various post processes along with age effectively leaving them almost welded in. BUT YOU BEST NOT DAMAGE THAT FINISH GETTING IT OFF! Anyway, making such a vise provides a very large contact surface an should be able to hold your pipe without marring or damage. And if you make it sturdy (perhaps 1" bolts, build from solid 4x4 stock, the sky's the limit) enough with enough clearance, grip is whatever you feel like putting into it. Eventually it will either hold it from turning, or swage it, but the latter could be made far more difficult to achieve by simply making the bushings longer. Eventually, it WOULD hold...
This is a very simple form that is very similar to mine, though being built for 2" bushings and from 2" square bar stock, I believe mine is a bit heavier.
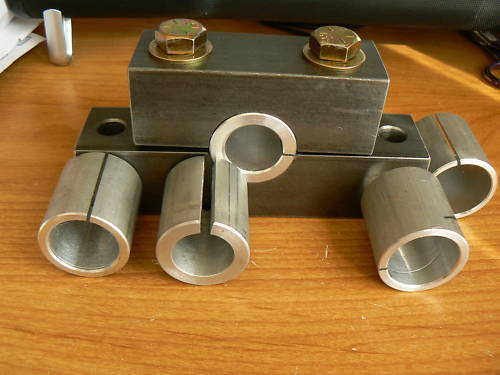
This is a very simple form that is very similar to mine, though being built for 2" bushings and from 2" square bar stock, I believe mine is a bit heavier.
Russ
Master Floor Sweeper
Master Floor Sweeper
-
- Posts: 302
- Joined: Mon Jun 25, 2012 12:13 pm
- Location: Wiltshire United Kingdom
Re: Avoiding Marring On Steel Pipe When Threading
OK thanks for that.BadDog wrote:I just recently posted in another VERY similar thread regarding what I have been told is called a "barrel vise", presumably in reference to removing rifle barrels without damage, and I'm told some of those verge on the impossible due to "clocking" and various post processes along with age effectively leaving them almost welded in. BUT YOU BEST NOT DAMAGE THAT FINISH GETTING IT OFF! Anyway, making such a vise provides a very large contact surface an should be able to hold your pipe without marring or damage. And if you make it sturdy (perhaps 1" bolts, build from solid 4x4 stock, the sky's the limit) enough with enough clearance, grip is whatever you feel like putting into it. Eventually it will either hold it from turning, or swage it, but the latter could be made far more difficult to achieve by simply making the bushings longer. Eventually, it WOULD hold...
This is a very simple form that is very similar to mine, though being built for 2" bushings and from 2" square bar stock, I believe mine is a bit heavier.
Re: Avoiding Marring On Steel Pipe When Threading
BTW, it certainly will work with a single split, the aluminum acting as a bushing sliding in the steel blocks. But for that reason, the steel blocks need to be bored near perfectly round (as on a lathe or with boring head, with gap spacer), and should be smooth polished inside. Otherwise the aluminum can't slide as it tries to close up on one side which may gall and/or reduce clamp force.
My preference is to fully split the bushing. That way there is not nearly so much sliding/moving required, and I have plain aluminum bar stock for making bushings, and wanted to use it "as is", which is not perfectly round or smooth, or even exactly on size. I could arrange the sizes so that I turn and bore each bushing, but I simply didn't think it was necessary for my needs so would be wasted work. The problem with split bushings is keeping each half matched, and worse yet, in place as you put things together. On the other hand, you don't have to slide the bushing from the end, which may be well away from where you want to hold, or may have features that prevent passage of the bushing.
Mine was (in part) for holding roll bar tubing up to 1.75", and that tubing may have bends or other tubes welded here and there, so single piece bushings are non-starters. As for the mild aggravation of installation, and not so mild if wrestling a larger tube weldment trying to get everything aligned. One thing I've found that makes life MUCH easier is to use studs instead of bolts. At least that all just sort of drops together and from that point it's not too terribly hard to manage with some planning and dexterity. I've imagined dozens of plans for somehow fixing/mounting the bushings to the blocks before attempting to mount the work piece, but as yet have not come up with anything I liked well enough to actually take the time to do the work. One of my criteria that makes it harder is that it must be some design that does not add substantially to the complexity of making and mounting the bushings. And I have more than once simply used some contact rubber cement.
My preference is to fully split the bushing. That way there is not nearly so much sliding/moving required, and I have plain aluminum bar stock for making bushings, and wanted to use it "as is", which is not perfectly round or smooth, or even exactly on size. I could arrange the sizes so that I turn and bore each bushing, but I simply didn't think it was necessary for my needs so would be wasted work. The problem with split bushings is keeping each half matched, and worse yet, in place as you put things together. On the other hand, you don't have to slide the bushing from the end, which may be well away from where you want to hold, or may have features that prevent passage of the bushing.
Mine was (in part) for holding roll bar tubing up to 1.75", and that tubing may have bends or other tubes welded here and there, so single piece bushings are non-starters. As for the mild aggravation of installation, and not so mild if wrestling a larger tube weldment trying to get everything aligned. One thing I've found that makes life MUCH easier is to use studs instead of bolts. At least that all just sort of drops together and from that point it's not too terribly hard to manage with some planning and dexterity. I've imagined dozens of plans for somehow fixing/mounting the bushings to the blocks before attempting to mount the work piece, but as yet have not come up with anything I liked well enough to actually take the time to do the work. One of my criteria that makes it harder is that it must be some design that does not add substantially to the complexity of making and mounting the bushings. And I have more than once simply used some contact rubber cement.
Russ
Master Floor Sweeper
Master Floor Sweeper
-
- Posts: 302
- Joined: Mon Jun 25, 2012 12:13 pm
- Location: Wiltshire United Kingdom
Re: Avoiding Marring On Steel Pipe When Threading
OK thanks even though I'm not a machinist or have any experience I think I get some of what you are talking about:)
Cheers,
Peter.
Cheers,
Peter.
Re: Avoiding Marring On Steel Pipe When Threading
Feel free to ask about whatever you don't understand. That's what this forum is for. It's a pretty safe bet that whatever your machining related question my be, someone on here knows the answer and is willing to share...
Russ
Master Floor Sweeper
Master Floor Sweeper